The Customer Service team will be unavailable on December 24 and 25. They will return to their normal hours on Thursday, December 26.
CloseProducing Accessible Positions: Quality Checks on Large Type Books
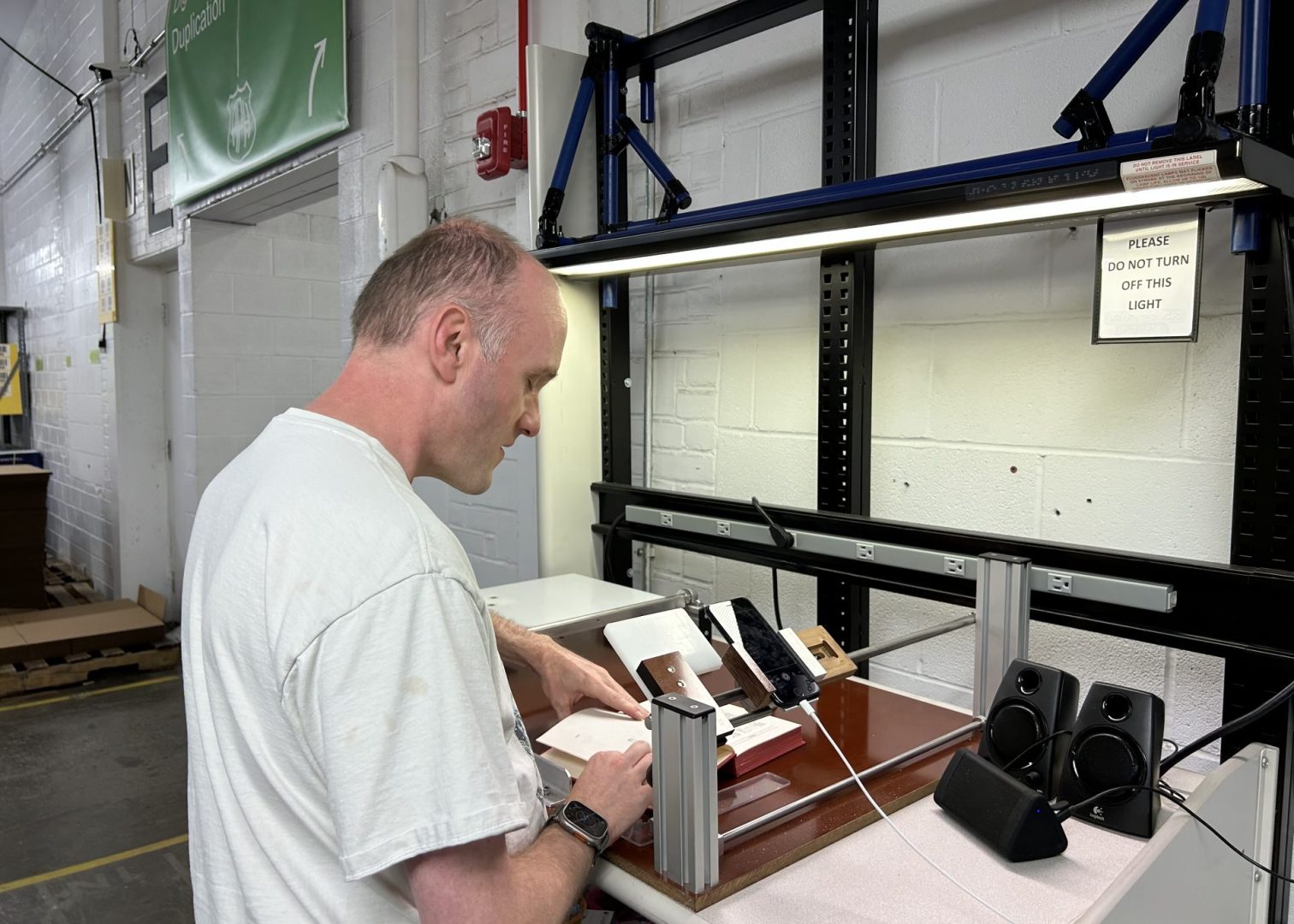
APH’s production department has raised the bar for barrier breaking in workplace accessibility. An openness to re-inventing job stations and routines has allowed for not only a streamline in production but has shown a willingness to listen and learn from employees.
Quality checks on large print materials are an essential part of the production process. At its simplest form, quality checking ensures pages are spaced correctly, figures are inserted in the right places, page numbers follow a correct sequence, and titles/headings are both legible and correct. In a braille edition, quality checks also include ensuring the braille on all the above pieces is correct. The process was entirely reinvented for Joey Couch. Joey was the first blind employee hired in quality and has opened the door for many more. Upon receiving Joey’s application for the quality check position, Anita Slaughter, Engineering and Quality Manager, as well as Brian Sellers, Maintenance Engineer, got to work on creating an accessible quality check system.
To make the position accessible, the team first needed access to reliable text readers. Joey uses three applications on a smartphone: Be My Eyes AI, VD Scan’s Optical Character Recognition, and Seeing AI. These programs can each be used to scan the physical book and copy before reading the text, page number, and figure information aloud. The Seeing AI program is also capable of recognizing page orientation and spacing in a way that can be shared out loud. The use of three distinct programs allows Joey to switch back and forth between them to use their individual strengths to his advantage.
These programs, while essential to the process, would not be beneficial without the physical set-up, built by Brian himself. Brian found materials within the floor and constructed an easy-to-use desk space for Joey. The set-up includes guide rails along the desk surface to ensure the book is properly positioned below the camera. On the left end of the desk, there is a white tray to hold extra materials. On the right end, there is a secure holder for the smartphone. It is connected by two metal arms at the side of the desk, with a rod across the middle. The rod holds a wooden clamp for the smartphone.
This design gives the user the ability to slide the phone horizontally across the length of the rod, as well as adjust the phone vertically for angle changes. There is a bright light above the desk to illuminate the text for easy detection by the phone programs. The setup gives Joey freedom to work independently and with ease. The intentional creation from the production team, paired with Joey’s adaptive, joyful, and can-do attitude, proved to be the perfect combination for a new kind of accessibility in the production workspace.
Joey’s set up was so successful, another accessible position was created using similar framing, for Jonathon McCarty, a Braillo Operator. Brian was able to build Jonathon’s station for what he estimates at only 30 dollars. Jonathon, who used to find it difficult to ensure page orientation and correct printing, finds that this new system gives him a greater level of independence and confidence in his workspace.
This is only the beginning for the Production team. According to Anita, the goal is to ensure every position on the braille production floor that can be, is made accessible. Brian believes achieving this goal will require “being creative and getting feedback from the blind and low vision community.” The developments in accessibility on the production floor are proof that where there is creativity and a willingness to include, those with blindness or low vision can excel in every space of the workplace.
Share this article.
Related articles
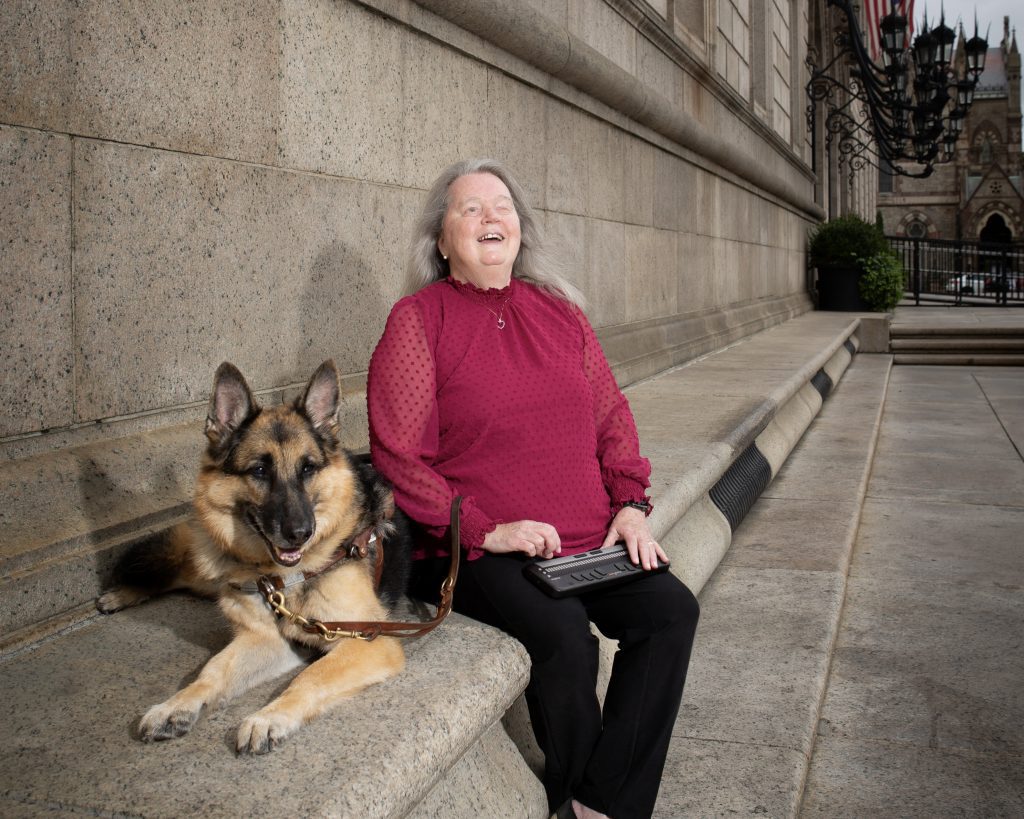
The Dot Experience Cast: Judy Dixon
Judy Dixon is a woman of humility, generosity, spunk, and drive. Judy worked for the National Library Service for the...
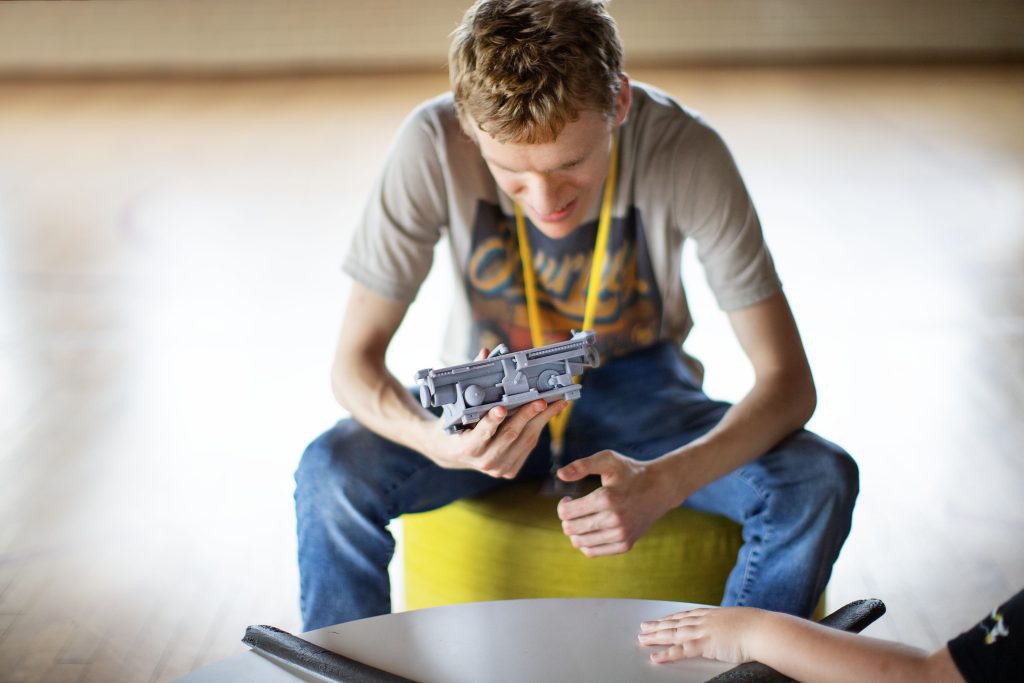
Solid Light Sets the Stage for Inclusivity
A lot goes into designing a brand-new museum. From exhibit planning, to selecting flooring, and beyond, our partners at Solid...
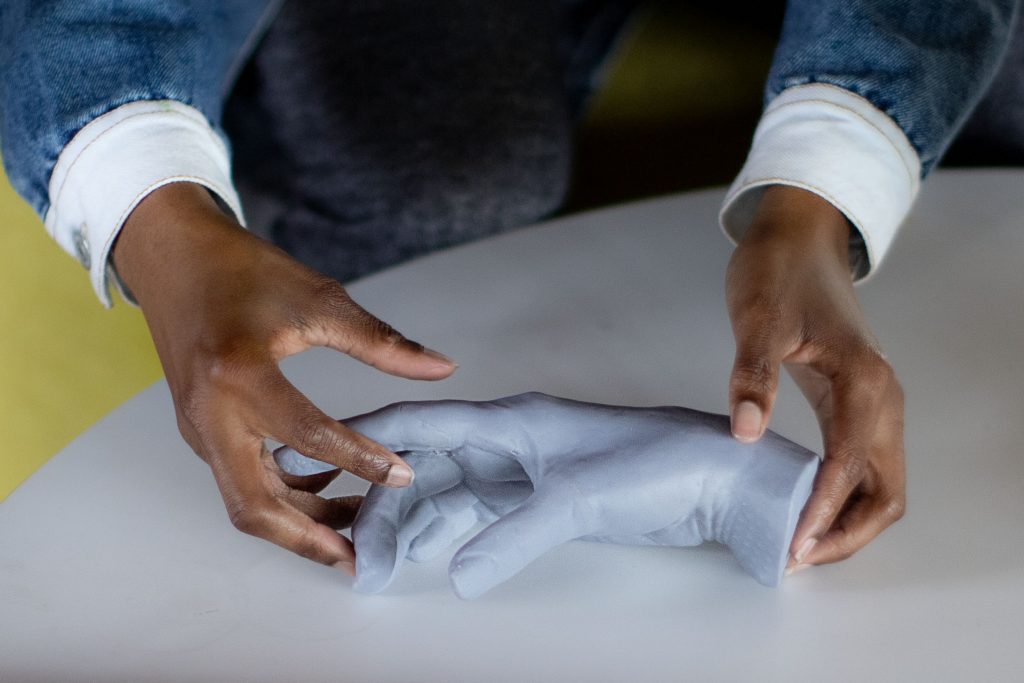
Designed to Include: The Dot Experience Begins with Accessibility
Every aspect of The Dot Experience, from the elevator shaft to the carpeting is being carefully planned, built, and tested...